協力メーカー 技術紹介
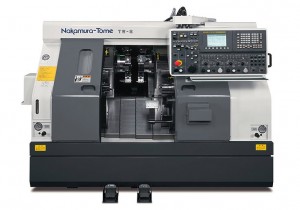
協力会社の加工機に稼働率の余裕が出ました。(2017年2月22日現在)
中村留 TW-8
2タレット、2スピンドル複合加工機
対向2スピンドル、L・R同時加工で時間短縮
棒材作業能力 (丸) op.42mm
主軸回転速度 6,000min-1
バー材供給機 3000mm
被削材は特に拘りません。
量産物に向いた機械です。
生産ロット 500個/月 ~
検査体制のしっかりした協力会社ですので、安心してお任せ頂けます。
お困りの方がいらっしゃりましたら、是非ともお声掛け下さい。
皆様からのお声掛けをお待ちしております。
(お問い合わせ先)
営業担当 : 坪谷・伊藤
HP http://mspjpn.com/
mail sales@mspjpn.com
電話 045-633-1056
2017年2月21日 8:21 PM | カテゴリー:切削加工, 協力メーカー 技術紹介
いつも、MSPブログに訪問頂きありがとうございます。
もう9月ですね。代表の伊藤です。
今日は、チョットへそ曲がりな投稿になります。
今回は「MSPは、面倒な商社です」と言う、???題名です。
PRが目的なのに、「面倒」なんて書いたら駄目でしょ!
普通は、そう思いますよね。
しかし、MSPは本当に面倒な技術商社なんです。
特に、初めてのお客様に対してはその傾向が高いです。
その理由は簡単です。
初めてのお客様は、当社を美味しく使う方法をご存じないからです。
MSPには素晴らしい協力会社から多くのサポートを受けながら営業活動
をさせて戴いております。
この協力会社群は、それぞれ特色があります。
同じ工法を採用していても、一番美味しい部分は千差万別です。
お客様が今まで経験された方法を基に設計された部品を、MSPでも
同じ様にご希望のコストで対応できるかはまた別の話です。
また、MSPは以下の様な公式でお客様へ最大限の付加価値をご提供
出来る様に努めております。
お客様 x (協力会社 x MSP) = 無限の可能性
この公式の大切な部分は、お客様も一緒に入っていると言うことです。
お客様のご協力無くして無限の可能性を追求する事は不可能です。
我々側だけで追いかける可能性は、ある意味において・・・
MSP側でも、お客様側でも、勝手に自己満足活動しているだけです。
三人寄らば文殊の知恵ではないですが、この公式には三人(社)が
入っているので色々な知恵が湧いてきて当たり前なのです。
どうか、一緒に考えさせて下さい。
どうか、一緒に考えて下さい。
我々は、お客様の喜びが無い限り、売上も利益も得られないと言う事を
身に沁みて感じております。
決して騙すとかそんな姑息な事はしません。
三社がバランスよく利益を得る中で、お客様の力が最大化する方法を
必死に考え提案させて戴きます。
なので、考えるための情報を出来るだけ沢山下さい。
情報が少ない依頼は、その仕事に対する入れ込み方が少ないのでは
無いでしょうか?
我々は常に全力で受注する為に考動します。
なので「見積りだけ取ろう!」的なニュアンスはどんなにオブラートに
包んでも感じてしまうんです。
また、情報が少なくても受注出来てしまった案件は、高い確率で
クレームが発生したりします。これは当然の結末ですね。
世の中では、景気悪化に伴いエゴ見積りが飛び交い始めました。
少しでも安ければ、他社へ転注する為の見積りです。
義理人情は通じない時代なのは知ってます。
でも・・・
MSPは、明確な理由のない既存品の見積りはお断りしています。
仮にコストダウンしたいのであれば、目標コストを提示して頂く様に
依頼します。
既存品には当然ながら現行コストがあり、コストダウン要求には
目標コストがある筈です。
コチラは、品質と納期をそのコストでクリア出来るか検討するのが
後々に問題を残さない検討方法です。
なので、指し値のない現行品切り替え見積りはお断りです。
それが例えP社やT社だとしても、この姿勢に変わりはありません。
新規立ち上げ品は、なるべく初期段階から、設計初期段階から
お声がけ戴ける様にお願いしています。
品質と納期を守れる最適な工法を選択し、適正なコストを追い求め
ないかぎり安い部品は手に入りません。
こんな風に、MSPってとっても面倒くさい技術商社です。
その分お付き合い戴ければ、総合的にお得な技術商社だと自負
しております。
こんな面倒な技術商社でよろしければ、是非ともお声がけください。
面倒くさい技術商社の代表 伊藤の戯れ言でした。
皆さまからのお問い合わせをお待ち申し上げております。
(取り扱い分野)
- アルミ押出形材に関する全ての加工
- 旋盤加工部品
- マシニング加工部品
- 複合加工部品
- ザス型によるプレス絞り加工
- 冷間プレス鍛造部品
- アルミダイカスト、アルミ鋳物
- 樹脂インジェクション成形
- ゴム成形
- 精密バネ
- 表面処理
- 組付け加工
(お問い合わせ先)
営業担当 : 坪谷・伊藤
HP http://mspjpn.com/
mail sales@mspjpn.com
電話 045-633-1056
FAX 045-633-1051
2016年9月1日 5:24 PM | カテゴリー:アルミ押出し材, イリサート, オリジナル商品, ゴム製品, ショットブラスト, ダイカスト, デジタルモールド, バフ仕上げ, ヒートシンク・放熱板, マグネシウムダイカスト, マグネシウム合金, 亜鉛ダイカスト, 代表のメッセージ, 切削加工, 協力メーカー 技術紹介, 外観仕上げ部品, 樹脂加工, 熱伝導度, 熱伝導率, 真鍮(黄銅), 社内加工, 簡易加工, 表面処理
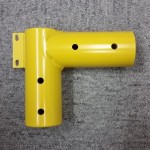
設備関連安全対策品
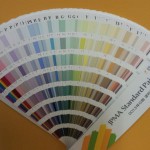
カラーパターン
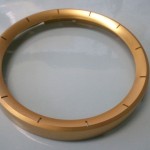
リング ゴールドアルマイト
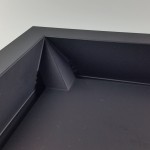
切削パス間隔 確認テスト塗装
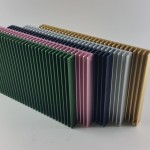
オリジナル商品 カラーアルマイト
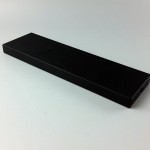
電子機器筐体 切削加工後に意匠性指定色塗装
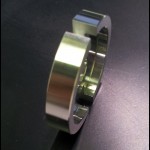
旋盤 鏡面仕上げ アルマイト加工
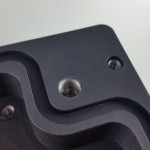
DMS5にブラックアルマイト、マスキング
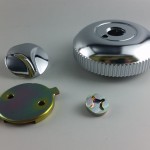
旧車レストア部品 アルミクロムメッキ、クロメート処理
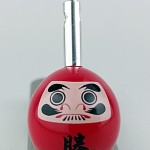
オリジナル商品 スタンプ印刷
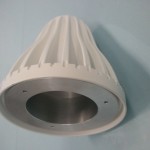
LED照明用ヒートシンク 切削サンプルへの塗装
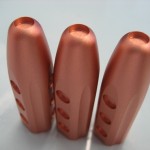
美容用品 切削後ショットブラスト、指定カラーでのアルマイト処理
2016年4月14日 11:13 AM | カテゴリー:ASSY加工, アルミ押出し材, オリジナル商品, ショットブラスト, ダイカスト, バフ仕上げ, 切削加工, 協力メーカー 技術紹介, 外観仕上げ部品, 表面処理
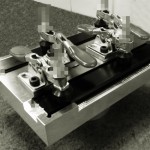
加工品の治具
いよいよ2月も終盤となり、3月末の期末に向けお引き合いを活発に頂いております。
お問い合わせ戴ける皆さんが一様に仰られるのが
「既存の協力会社さんがキャパオーバーしていて・・・ 」
と言う事で、お困りだとご連絡を戴きます。
MSPでは、優良工場100社を超える協力会社と連携しております。
決して余力のある訳ではありませんが、出来る限り対応させて戴ける様に
協力会社の受注状況を日々確認しながら営業活動を行っております。
決算に向け、追い込みでお急ぎの加工品など御座いましたら、遠慮無く
お問い合わせ下さい。
全てが対応出来るとは言えませんが、出来る限りの対応をさせて戴きます。
材料調達から、表面処理までワンストップサプライ可能なMSPへお任せ下さい。
皆様からのお問い合わせをお待ちしております。
(お問い合わせ先)
営業担当 : 坪谷・伊藤
HP http://mspjpn.com/
mail sales@mspjpn.com
電話 045-633-1056
FAX 045-633-1051
2016年2月26日 7:27 AM | カテゴリー:アルミ押出し材, ヒートシンク・放熱板, 切削加工, 協力メーカー 技術紹介, 樹脂加工, 真鍮(黄銅), 表面処理
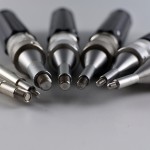
イリサート 挿入治具
本日は、アルミ材の加工品における タップ穴の「ネジ孔強化用埋込みナット」の話を書かせて戴きます。
「ネジ孔強化用埋込みナット」と言えば従来、一般的には断面図が菱形のステンレス鋼線をスプリング状にした「ヘリサート」等の名称の製品をお使いの方が多いと思います。
「ヘリサート」はスプリング鋼線を専用タップ溝に挿入しますが、鋼線の一部でも専用のタップ溝に入っていないと、ピッチ飛びが発生し、内径タップ穴が形成できません。
また挿入後工具引っかけ部であるタングを折る必要があり、その時スプリング自体を変形させる作業ミスが起こりやすく、挿入不良等トラブルの原因となっていました。
また、挿入には熟練を要する事がトラブル誘発原因となっていす。
そんな数種類の問題点を解決出来る代替え品としてMSPが推奨して居るのが、有限会社廣杉精機社製「イリサート」と呼ばれる製品です。
なぜ推奨しているかと言えば「信頼性」という点に尽きます。
この製品の特長は、内外形共にネジ構造なのでピッチ飛びの心配はありません。
タング折りによる作業ミスも発生しません。
挿入も熟練を要せず、極端に言えば小学生でも間違いのない作業が行えるほど簡単に挿入できます。
挿入用の下穴タップは、市販の一般的な工具で行えます。
一体構造の為、繰り返しネジの脱着を行ってもヘリサートの様にバネ伸びで使用出来なくなる事もなく、緩んではいけない場所ではネジの緩み止の塗布も可能です。
メーカーが作業手順をYouTubeで公開しておりますので、参考までに貼り付けておきます。
https://youtu.be/F5lzYNatfjY
また対応サイズも豊富にあるので、最適なサイズでネジ穴強化が可能です。
信頼性という点では、例えば、自動車部品(自動車。二輪車)、輸送機器(船舶・航空機、鉄道)、宇宙産業、印刷機械、事務機器、医療機器、通信機器、電気・電機・電子機器、繊維機械、映像機器(カメラ・三脚)、農業機械、楽器、遊具(ラジコン・ロボコン)などでの採用実績が有りますので、問題ありませんし、現にMSPで作業させて戴いた部品は一度の挿入ミスもなく、お客様でのご使用時にもなにも問題が起きておりません。
一つだけ問題なのは、専用の挿入治具が必要になることです。
MSPでは、 標準の挿入治具だけではなく、狭小深穴専用の挿入治具を特注しお客さまのニーズに合った対応を取らせて戴いております。
「ネジ孔強化用埋込みナット」の必要な部品をオーダーされる場合には、是非ともMSPまでご一報下さい。
社内で作業し、品質検査も含め万全の対応を取らせて戴きます。
皆様からのお問い合わせをお待ちしております。
(お問い合わせ先)
営業担当 : 坪谷(ツボヤ)
HP http://mspjpn.com/
mail sales@mspjpn
電話 045-633-1056
FAX 045-633-1051
2016年1月18日 2:08 PM | カテゴリー:ASSY加工, アルミ押出し材, イリサート, ヒートシンク・放熱板, 切削加工, 協力メーカー 技術紹介, 樹脂加工, 社内作業, 社内加工, 簡易加工
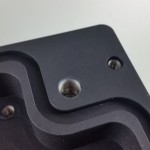
アルミ鋳物 切削ヒートシンク
アルミ鋳物からの切削ヒートシンクは、当社へお任せ下さい。
鋳物素材の調達、切削加工、表面処理、ネジ孔強化ナット組み込みまで一貫し、一個からでも対応可能です。
ヒートシンクに求められる放熱性能をクリアする為、高熱伝導率素材(HT-1等)の鋳物も対応しております。量産を前提とした試作の場合は、ADC12からの切削も行っております。
「ネジ孔強化ナット」に関しては、イリサート(R)を推奨しております。
従来一般的に使用されて来た「ヘリサート」に比べ、ピッチ飛び、タング折り時に発生しやすいスプリングの変形などが起こらず、安定的に高強度・高精度な補強が可能で、弊社内においてロックタイトも塗布し確実な挿入作業を行います。
また、表面処理に関しては鋳物の処理を得意とする協力会社と協業し対応しており、指定箇所には丁寧にマスキング処理を行い通電性を確保する事も対応しております。
さまざまなご要求にお応えずべく、各工程ごとにスペシャリストと言える協力会社と連携し、対応させて戴きます。
アルミ押出し材を利用した櫛型ヒートシンク、アルミ板材から削りだす全切削ヒートシンク、量産のアルミダイカストヒートシンク、板金加工による放熱板等々、アルミに限らず無酸素銅を利用した高効率ヒートシンクなど、放熱性能を必要とされる部品を一貫して対応させて戴きます。
「どんなことが出来るのか聞きたい」「こんな事が出来ないか?」「従来品のコストダウン方法は無いか?」という方は、お気軽にお問い合わせ下さい。
お急ぎの方は、迷わずお電話下さい。
四半世紀ヒートシンク一筋、ベテランの技術営業担当が皆様の疑問にお答え致します。
皆様からのお問い合わせをお待ちしております。
(お問い合わせ先)
放熱関係営業担当 : 坪谷(ツボヤ)
HP http://mspjpn.com/
mail sales@mspjpn
電話 045-633-1056
FAX 045-633-1051
2015年11月4日 10:00 AM | カテゴリー:ASSY加工, アルミ押出し材, ダイカスト, ヒートシンク・放熱板, 切削加工, 協力メーカー 技術紹介, 材料について, 社内加工, 表面処理, 難削材について
旋盤系の加工品をお引き合い頂くと、内径キー溝加工の指示が
記載されて いる事がよくあります。
歯車やボスになるであろう部品。
キー溝加工する際に使用される加工設備は、大きく分けて2種類。
・ブローチ盤
刃が鋸状に配置された長尺の刃物を「引き抜く」事により被削物を
加工する切削加工の一種。
仕上がり部分の寸法が、加工に使用したブローチと、ほぼ同じと
なるため、フライス盤・形削り盤などによる加工より高精度に
仕上がる上、加工速度が速い。
また、繰り返し精度が高いのが特徴で、大量生産に向いています。
・スロッター
スロッターとは立て削り盤ともいわれ、溝削り加工を行う工作機械の
ことをいいます。
水平2軸直線運動および回転運動を間欠的に行う円テーブル上に
加工品を取り付け、垂直運動するラムに取り付けたバイトを
使用するのが特徴です。
主にキー溝、スプライン、角孔、インボリュートスプライン等を加工します。
先日お問い合わせ戴きました案件では、コスト面でお困りとの事で
詳しくお話を伺ってみますと、スロッターで対応していると思われる
情報を出して頂きました。
加工寸法的には、ブローチ盤の既存刃物があればコストが確実に
下る 事が予測できました。
記憶では、仲間の会社がJS9規格で幅3~14mmまでを1mm単位で
取り揃えていた筈なので、早速問い合わせ。
その結果、数点の微細な問題はあったのですが、ご要望サイズの
刃物がありそれで対応可能という結論に至りました。
この様に加工法の選択を正しく行い、その道のプロと巡りあえば
コストを適正に下げることも可能です。
弊社ではこの様に適正な加工法を選択する事で、品質を落とさずとも
コスト競争力を保つことが出来ると考えています。
国内メーカーの技術力を有効活用する事で、日本の未来にものづくり を
残していく第一歩だと思います。
そして、弊社のような立場で加工法をコーディネートする人材の育成が
モノづくりの現場に適正な利潤を生み出す為に必要な事と手前味噌
ですが思っています。
今回は、キー溝加工を例にお話致しましたが、適切な加工法に変更する 事で
お客様の利益に繋がる事例は多いです。
品質・納期・コストでお困りの際には、弊社へ気軽にお声がけください。
ご連絡をお待ちしております。
「お問い合わせ」はこちらをクリック!
2015年3月26日 3:26 PM | カテゴリー:協力メーカー 技術紹介
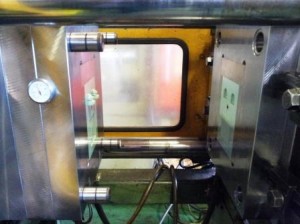
デジタルモールド(Digital Mold)
デジタルモールド(Digital Mold)専用の大きなサイズのモールドベースが完成し、成形TRYを行う為に現場で立ち会ってきた。
デジタルモールドとは、業務提携先の有限会社スワニーによる、製品入れ子部分をストラタシス社のObjet260 Connex™で成形した型で樹脂インジェクション型を作る技術の名称。
前回の記事 http://mspjpn.com/digital-mold.html
誤解のないように先に書かせていただくが、この技術は金属の金型が必要なくなる技術では無いと言う事。
あくまでも、量産と同じ材質で同様の成形プロセスによるサンプル作成を行う事により、開発段階での様々な評価や実験のリードタイムを短縮し、開発スピードをあげられるツールに成り得るのでは無いかと試行錯誤を繰り返している段階。
そんな背景を受け、日経新聞への掲載による反響で得られたニーズの具現化を目的とする今回のTRY。
今回のTRY形状は、平面にレンズカットを施しアクリルで成形出来るかの検証と、合わせ面を持つ3D形状の精度確認。
この立ち会いにはストラタシス社の社員も立ち会い、その状況をご確認頂いた。
まずは、平面のレンズカット品。
流動を確認するため、流れの良い軟質の材料を用いてTRY。
レンズカットへの転写もスムーズで、本命のアクリルにも期待を抱かせる滑り出し。
しかし、樹脂で樹脂を整形する技術はそんな簡単な事ではなく、成形機の微妙な注入圧力コントロールも必要。
金属金型でアクリルを整形するときの温度条件とは異なる所も、大きなポイントです。
結果は、思った以上にレンズカットの面が抵抗になり、デジタルモールド側に影響を与えている事が判明しました。
TRY形状は、通常の金属金型と同じモノを想定していたので、最初のTRYにしては、思ったよりも流れたと言うのが、参加メンバーの感想でした。
また、合わせ面を持つ3D形状の方は、パーティングライン(型合わせ面)をどこまで圧力との兼ね合いでコントロール出来るかをTRY。
こちらも、ランナーとゲート位置が圧力の上昇とともに影響が出る事が判明し、実験結果としては良いデータを取ることが出来ました。
この様に、新しい技術を開発していくには様々な検証を重ね、TRY&ERRORを繰り返しデータを積み重ねる必要があります。
MSPでは、業務提携会社の有限会社スワニーと共に、デジタルモールドの技術を更に高め、より多くの皆様に、開発スピードのアップと言う成果をお届け出来るように努力していきたいと思います。
デジタルモールドに関するお問い合せは
株式会社エムエスパートナーズ
担当 伊藤
メール sales@mspjpn.com
電話 045-633-1056
まで、お気軽にお問い合わせ下さい。
2013年11月28日 11:20 AM | カテゴリー:デジタルモールド, 協力メーカー 技術紹介, 材料について, 樹脂加工
業務提携先の会社が、素晴らしい技術を開発致しましたのでご報告します。
樹脂成形の技術で、専用にはなりますが従来のモールドベースと同じ構造で、製品入れ子部分のみデジタルツールを利用して金型を製作する「デジタルモールド」という技術です。
業務提携先 : 有限会社スワニー (長野県伊那市)
日本経済新聞で紹介された記事を掲載します。
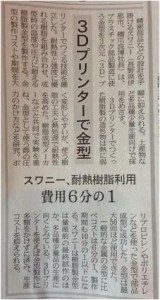
デジタルモールド新聞掲載記事
開発スピードが問われる時代に、設計評価段階で量産と同じグレード樹脂で形状化が安価に出来れば・・・という事で協力会社が独自に実験しており、3Dプリンター世界シェアトップのストラタシス社製のObjet 260 connexの耐熱造形樹脂を利用することで、今回の技術開発のトライを行ったとの事です。
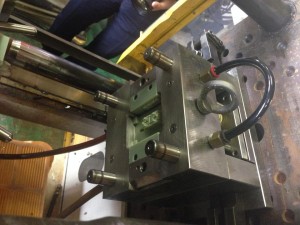
デジタルモールド入れ子
この画像の製品入れ子部分は、3Dプリンターによる造形と造形サポート除去で5時間ほどで完成しました。
金型への組み込みや調整などは、1~2日ほどで出来ましたのでリードタイムは通常の金属入れ子に比べると驚くほど短縮できおります。
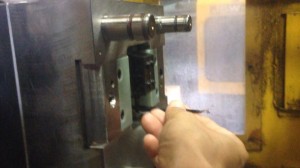
デジタルモールド成形トライ
やはり、成形条件は通常の成形と同じようにとはなかなか行きませんが、この短時間で量産と同じ材料で部品形状確認できるのはデザイン担当の皆さんや、設計者様としては画期的ではないでしょうか。
今回の形状ではスライドコアも可動させて深いリブなども設けてみたのですが、しっかりエジェクターで型離して成形ができましたが、外観はヒケやバリでまだまだ研究が必要な様です。
10月初旬、大坂での展示会で金型を展示したので、初回トライでは無理をせずに、材料はPP、POM、ABSの3材料で合計30ショットほど成形したとの事。
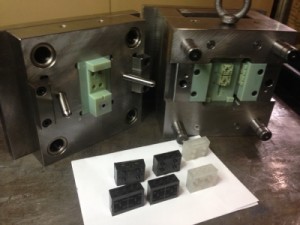
デジタルモールド入れ子と製品
提携先曰く、今後の課題は、型強度を考慮しながら成形圧力や樹脂温度をどこまで上げる事ができるか、入れ子形状の工夫で型強度の向上など課題を持って取り組むと意気込んでいます。
また、現在のテスト用モールドベースの他に、もう少し大きなサイズのテストも行える様にモールドベースを手配中です。
製品の拡大写真も掲載しますね。
けっこう深リブも出来ていて、いろいろな面で活用して戴ける筈だと感じております。
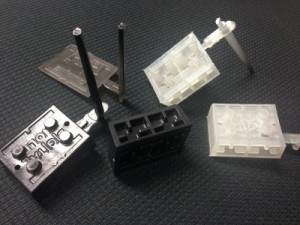
デジタルモールド 試作品写真
MSPの手元にトライ品があります。
まだまだ勉強しなければならない事が多いのですが、ご興味のある方はお声掛け戴ければご説明に上がりますので、お気軽にお問い合わせ下さい。
その際には「デジタルモールド」の件でとお申し付け下さい。
2013年11月1日 9:00 AM | カテゴリー:デジタルモールド, 協力メーカー 技術紹介, 材料について, 樹脂加工
非鉄金属 電縫管の特徴は、その高精度・高品質にあります。
そもそも電縫管は、肉厚一定な圧延板を管状に丸め、その継目を溶接して製造されます。
そのため、押出管に必ず発生してしまう「偏肉」が皆無になるパイプの製造が可能です。
肉厚が均一なだけでなく、内面精度や寸法公差においても高く評価され、先端分野
精密分野に幅広く採用されています。
また、板厚2mmまでの厚肉の電縫管も製造可能であり、従来の押出管で懸案となって
いた 精度や偏肉などの品質問題が、電縫管に置き換えることにより解決できます。

非鉄金属 電縫管は精度だけでなく、強度においても優れた信頼性があります。
MSPの協力会社では、高周波溶接の溶融部分を出来るだけスクイズアウトし、ビードカット
することにより、 欠陥が発生しやすい部分を皆無にした電縫管を製造しております。
溶接部分があるために、強度を懸念されることもありますが、押出管との比較試験の検証結果
では、脆弱性の心配がないというデータが得られています。

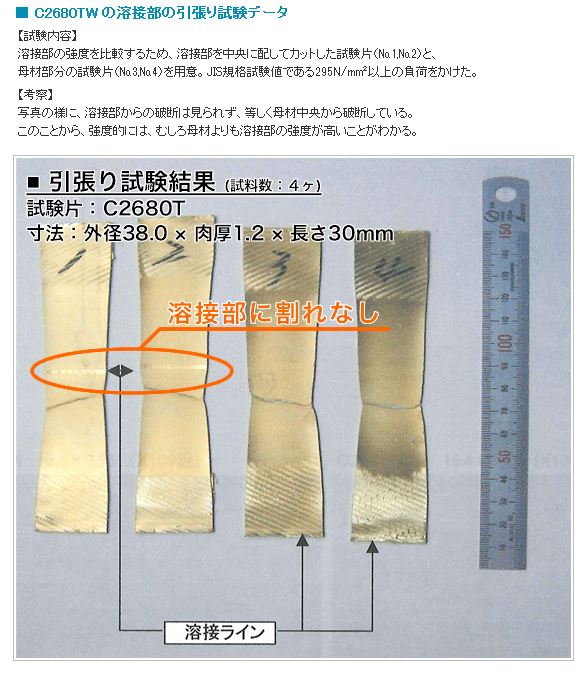
精密微細・肉厚均一という電縫管の特性を活かし、使いやすい強度伸びを設定、寸法許容差
も 厳密に製作しております。
異形管、極細管、特殊仕様管などの製品を、検査・測定機器といった精密分野や、パソコン用
レーザープリンターの感光ドラム、 電気自動車用次世代のリチウムイオン バッテリーケースなど
先端分野に実績があります。
MSPの協力会社は、地道な技術力蓄積により、特に通信分野向の特殊管について、国内でも
他の追随を許さない技術力を有しています。
チタン合金パイプは、その生体適合性により、医療用インプラントや人工骨などに活用されています。
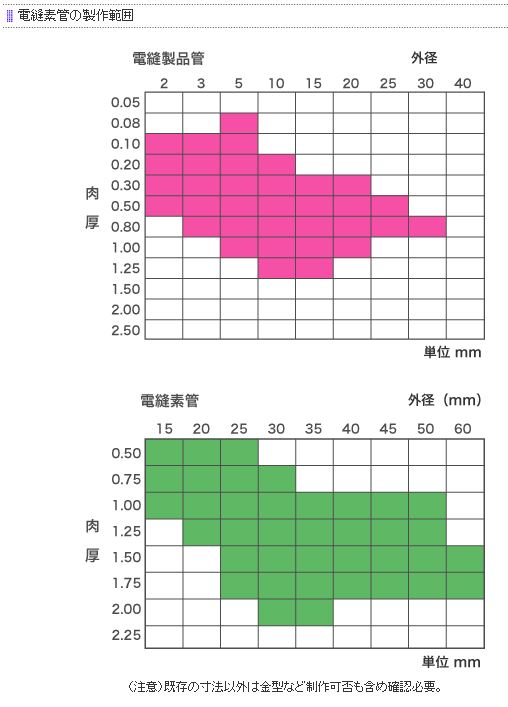
2013年7月18日 9:00 AM | カテゴリー:協力メーカー 技術紹介, 材料について, 真鍮(黄銅)
« 前のページ
次のページ »